MachIVshooter
Member
Kinda had one like this in mind for a bit, even before the single shot pistols or 9mm pack rifle, but was still working out the idea in my head. Well, I finally decided to get into CAD with Fusion 360, and that kinda helped get the ball rolling on this one, giving me a tool that aids in seeing the thing with actual eyes rather than mind's eye before cutting material. Still learning, but I can see that it'll be a useful tool, especially once I better learn to use the animation functions.
Anyway, the idea was to to make the lightest possible take down repeating .22 with the equipment I had, very compact, pretty tough and highly weather resistant. So, the only carbon steel parts are the barrel, extractor and springs, everything else 7075-T651 aluminum, 6Al-4V titanium, 18-8 stainless, 416 stainless, carbon fiber and ABS plastic.
This is my first build using CAD, and while I did not and will not design every single part before building, I did do the major components, and it has helped a bit. These are the CAD renderings of the receiver, chassis, bolt, bolt tail and barrel extension:
Unlike typical rimfires, this rifle uses a centerfire style twin lug bolt which engages the extension. It is also a cock on close design like an SMLE. The cartridges are stripped from the magazine by the left bolt lug, which is relieved slightly for the feed lip, and sits about 15° clockwise of vertical orientation when the bolt is open. The barrel is threaded into the extension (3/8-24 NF). I had to weld material onto the barrel and then turn it to create a stop point, which can be seen here with the actual physical parts:
Receiver is 7075-T651 aluminum. The bolt body, tail and handle are all 6-4 Ti, as is the barrel extension. The tail threads into the body (3/8-40 NEF). My original plan was for the handle to also be thread only, but there was so little engagement that I decided to TIG weld it to the body. (P.S.-I'm not a master welder, but before judging my welds, please bear in mind that the bolt handle is just 1/4" diameter where it meets the bolt, and the bolt body walls only .095" thick, so heat is an issue, making blending out beads a challenge):
The chassis is nearly complete, and has been a pretty tricky part on manual equipment, with lots of rotary table work, rotary indexer, and tilt/swivel vise set up:
Carving it out to house the receiver was also arduous, much of it done by hand with small chisels and files due to the inside square corners that are impossible to mill
After profiling the receiver, I broached the bore for the bolt lugs with the bolt itself (before welding the handle on), then used the tilt/swivel vise to cut the handle channel
And this is where we're at now, just needing striker, trigger, sear, mag catch and a few other small parts and cuts:
And taken down:
The height of the buttstock to the receiver looks a little awkward, but it's actually not bad at all when holding the thing. Can either use a low cheek weld, or rest your cheek on your firing hand, just behind the thumb.
The barrel assembly will be held to the receiver with a simple stainless sheet metal clip that engages the Picatinny slots.
Is 31.25" with a 16.5" barrel. 16.5" long, 5.4" tall and 1.25" wide at the receiver when the bolt knob is up in the stowed configuration. Current weight is 18.2 ounces, which I expect to increase to 20.7 with the additional parts, very close to my 20 ounce goal
Anyway, the idea was to to make the lightest possible take down repeating .22 with the equipment I had, very compact, pretty tough and highly weather resistant. So, the only carbon steel parts are the barrel, extractor and springs, everything else 7075-T651 aluminum, 6Al-4V titanium, 18-8 stainless, 416 stainless, carbon fiber and ABS plastic.
This is my first build using CAD, and while I did not and will not design every single part before building, I did do the major components, and it has helped a bit. These are the CAD renderings of the receiver, chassis, bolt, bolt tail and barrel extension:
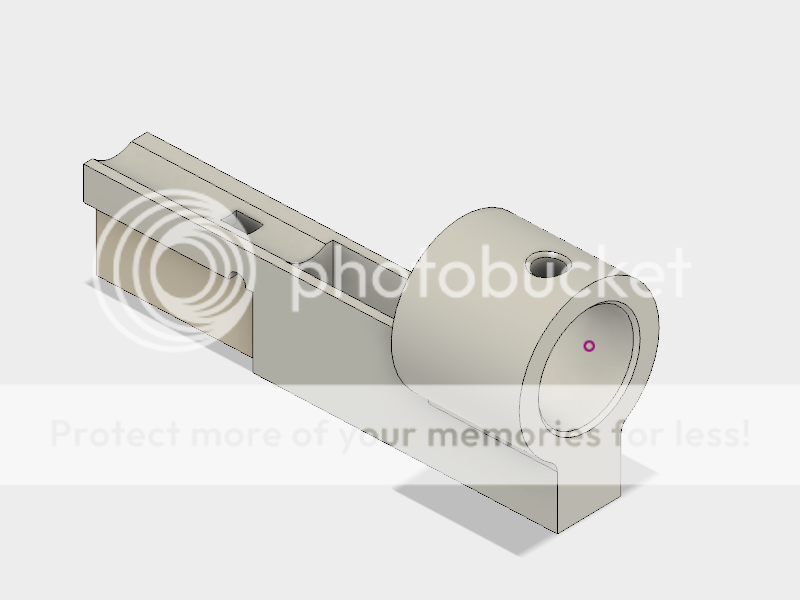
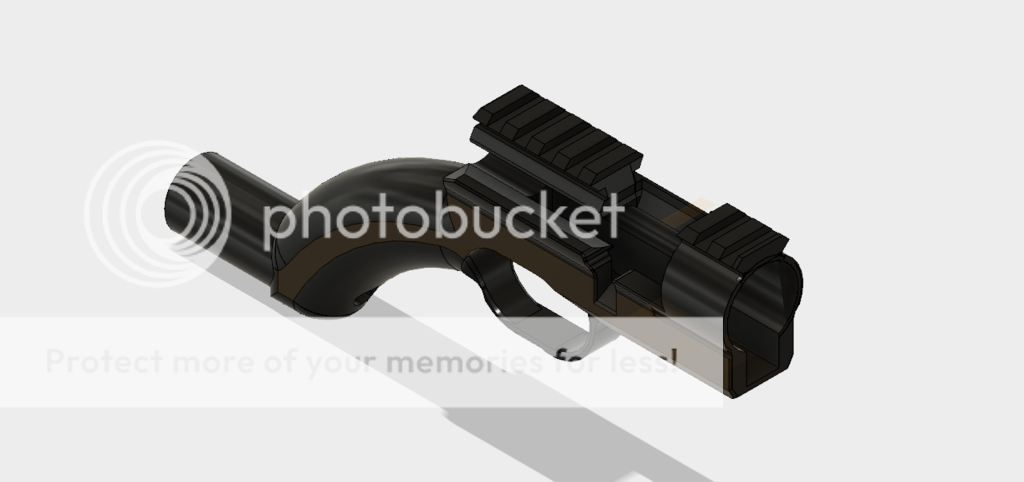
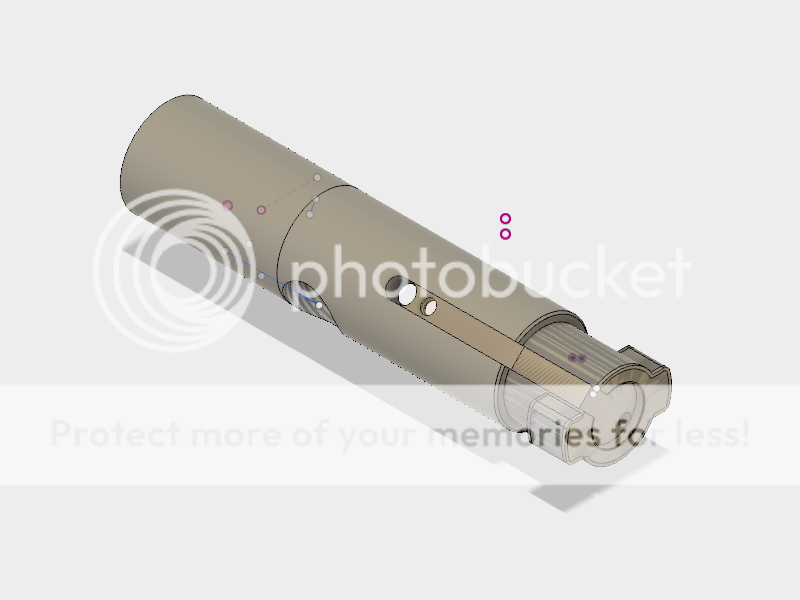
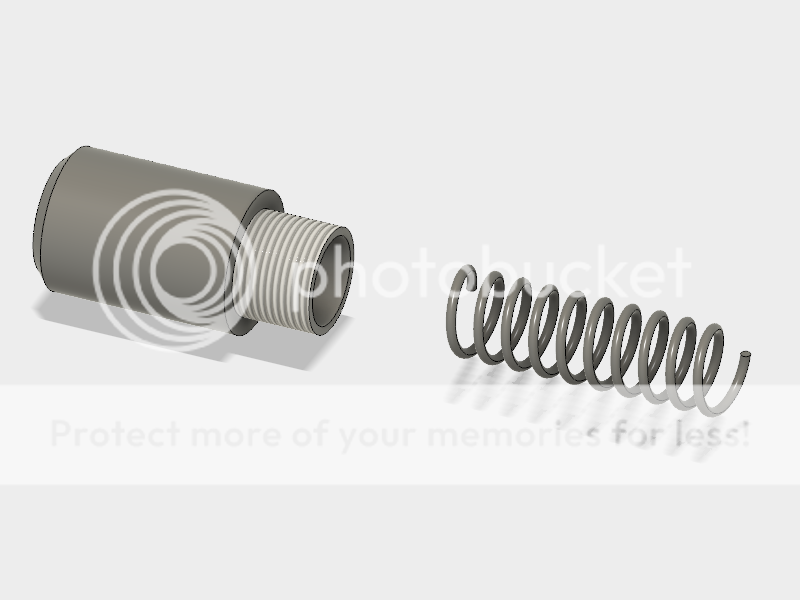

Unlike typical rimfires, this rifle uses a centerfire style twin lug bolt which engages the extension. It is also a cock on close design like an SMLE. The cartridges are stripped from the magazine by the left bolt lug, which is relieved slightly for the feed lip, and sits about 15° clockwise of vertical orientation when the bolt is open. The barrel is threaded into the extension (3/8-24 NF). I had to weld material onto the barrel and then turn it to create a stop point, which can be seen here with the actual physical parts:
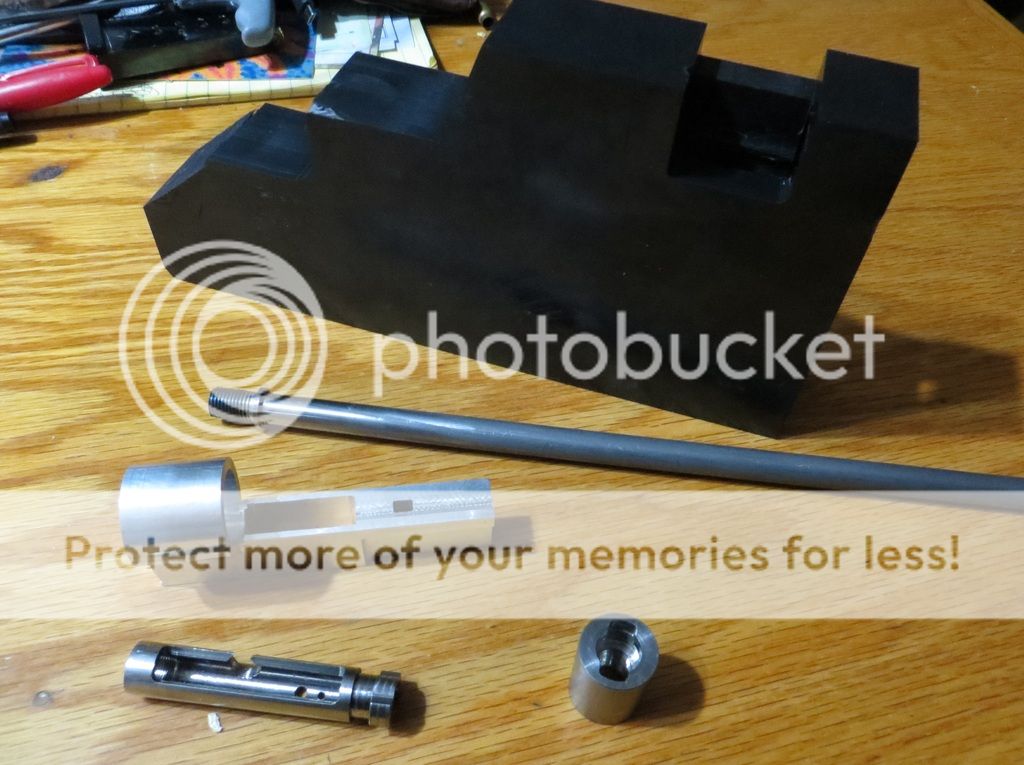
Receiver is 7075-T651 aluminum. The bolt body, tail and handle are all 6-4 Ti, as is the barrel extension. The tail threads into the body (3/8-40 NEF). My original plan was for the handle to also be thread only, but there was so little engagement that I decided to TIG weld it to the body. (P.S.-I'm not a master welder, but before judging my welds, please bear in mind that the bolt handle is just 1/4" diameter where it meets the bolt, and the bolt body walls only .095" thick, so heat is an issue, making blending out beads a challenge):
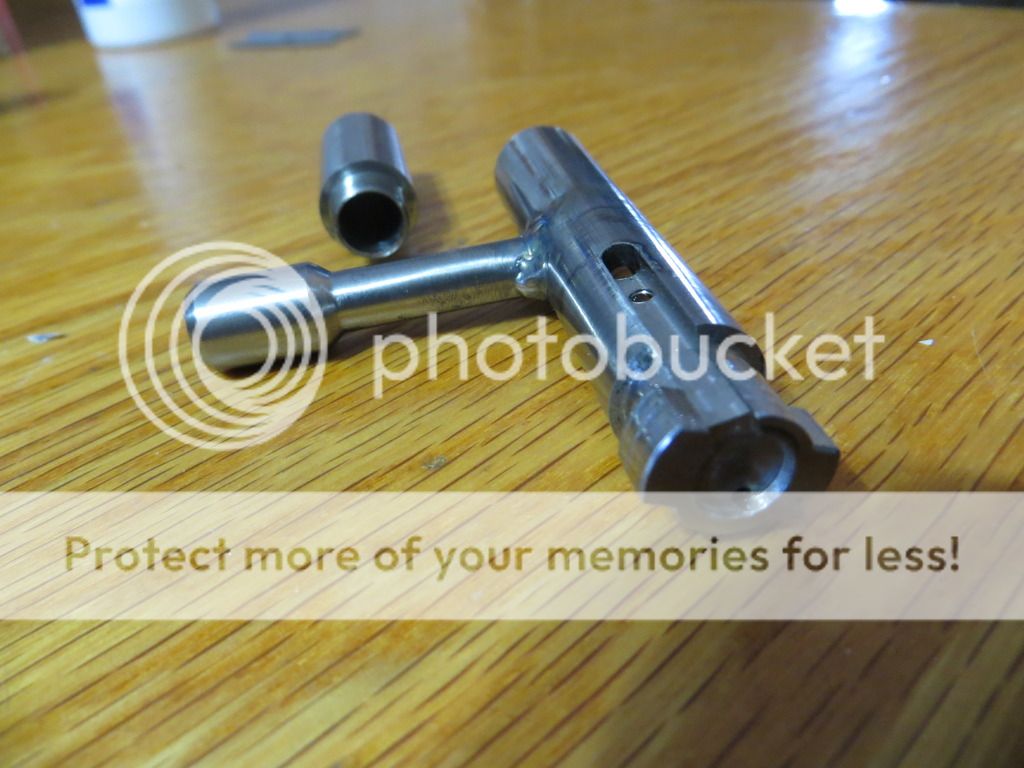
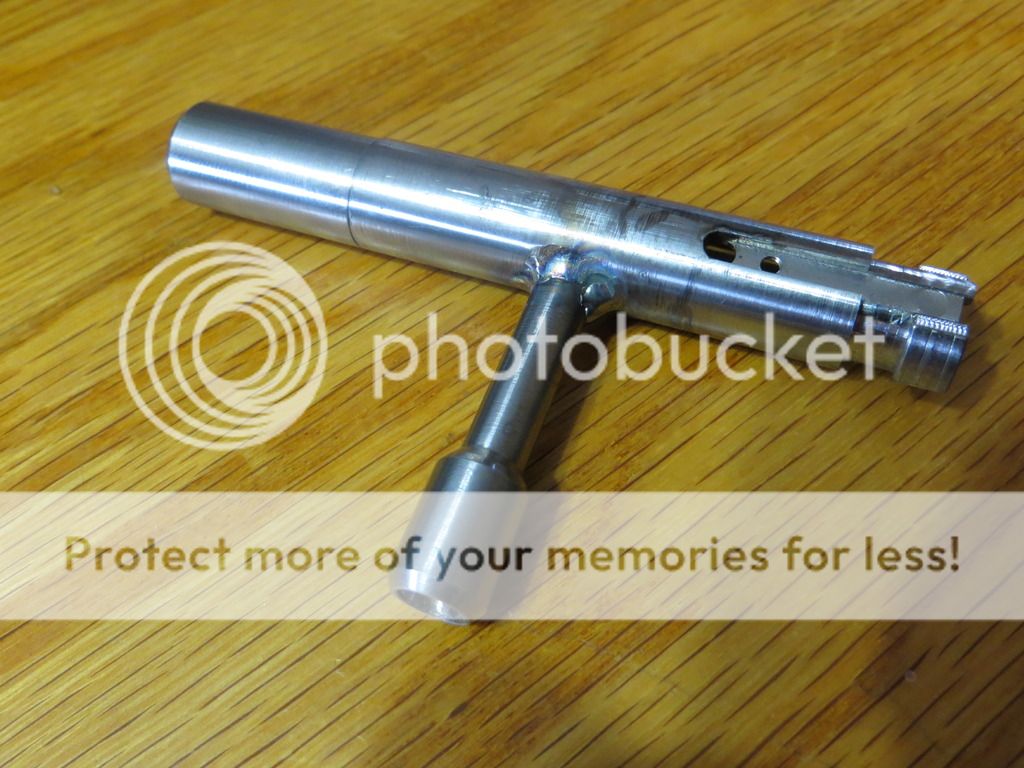
The chassis is nearly complete, and has been a pretty tricky part on manual equipment, with lots of rotary table work, rotary indexer, and tilt/swivel vise set up:
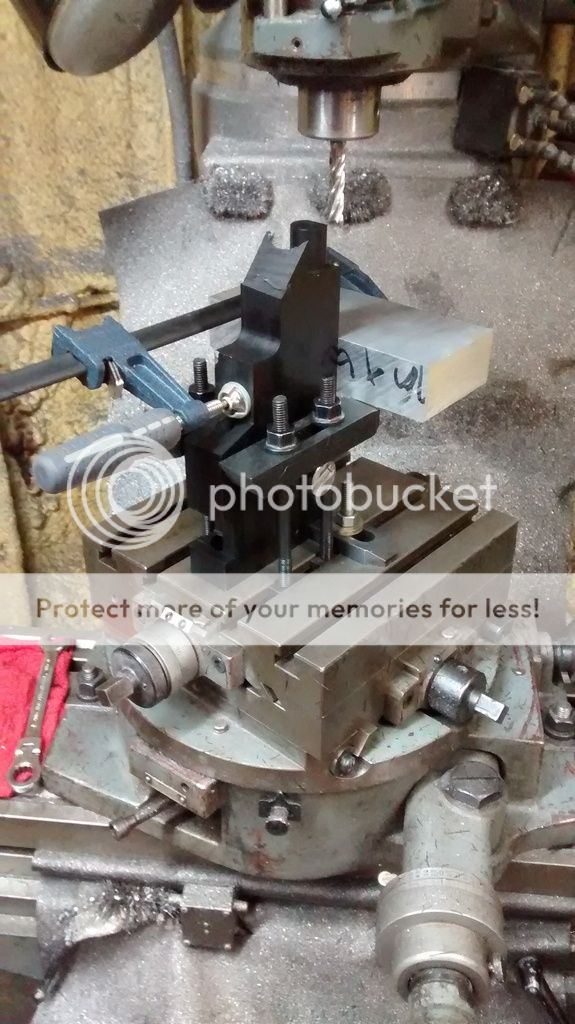
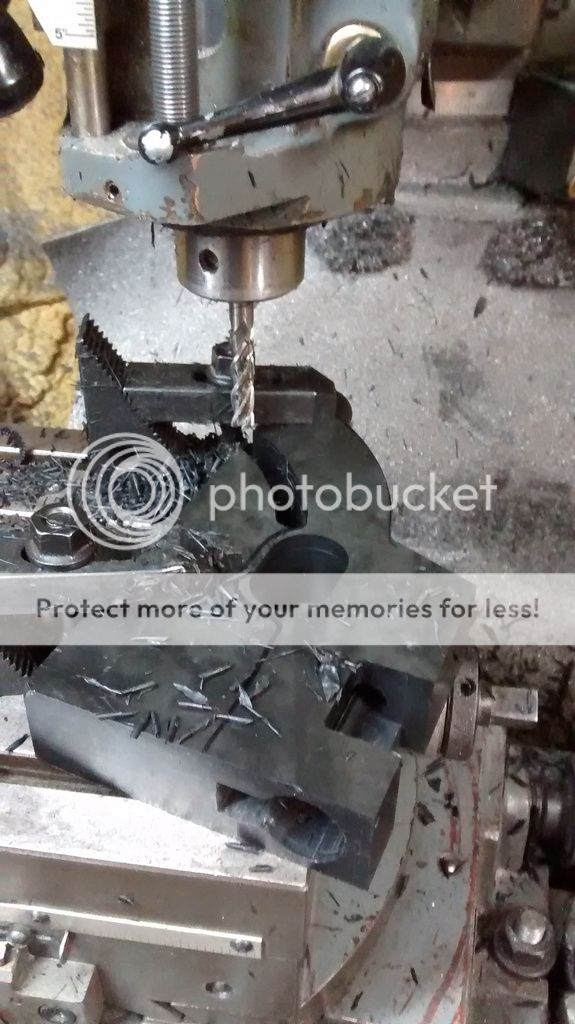
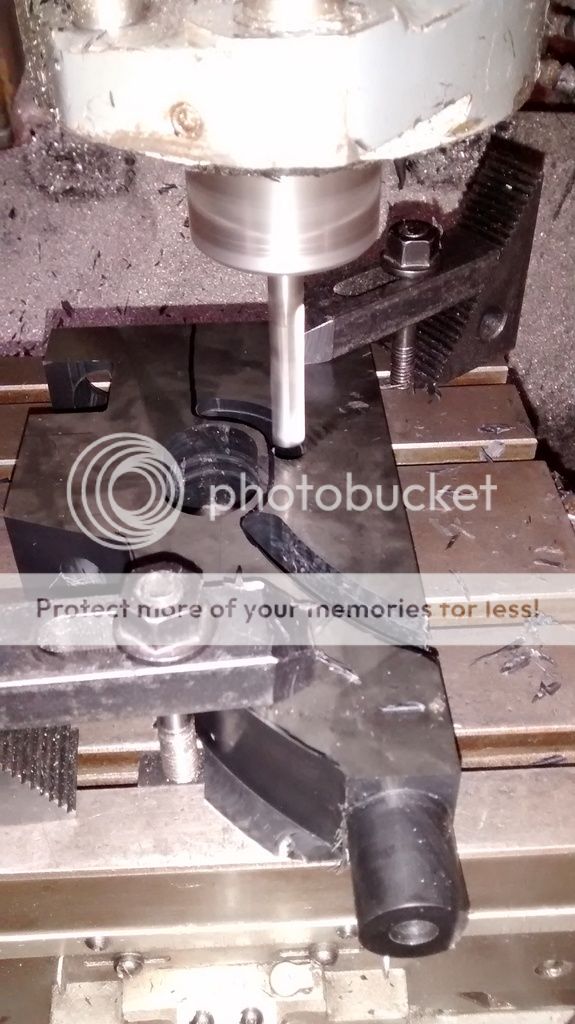
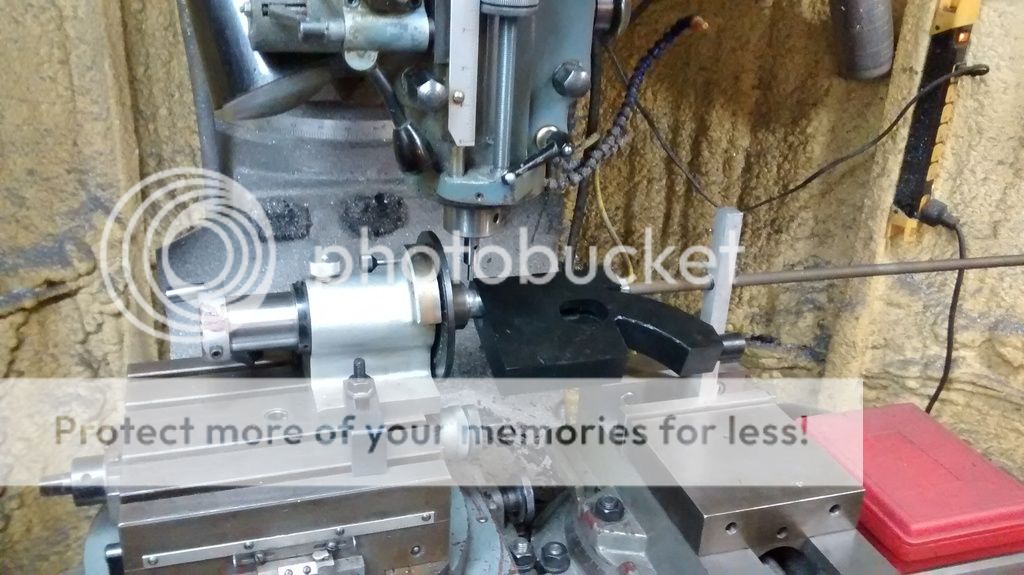
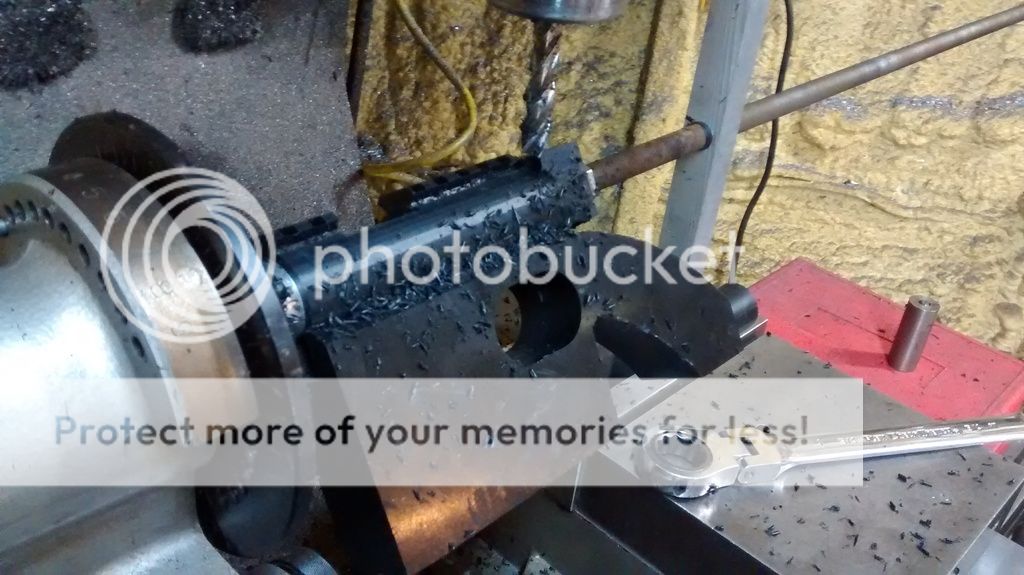
Carving it out to house the receiver was also arduous, much of it done by hand with small chisels and files due to the inside square corners that are impossible to mill
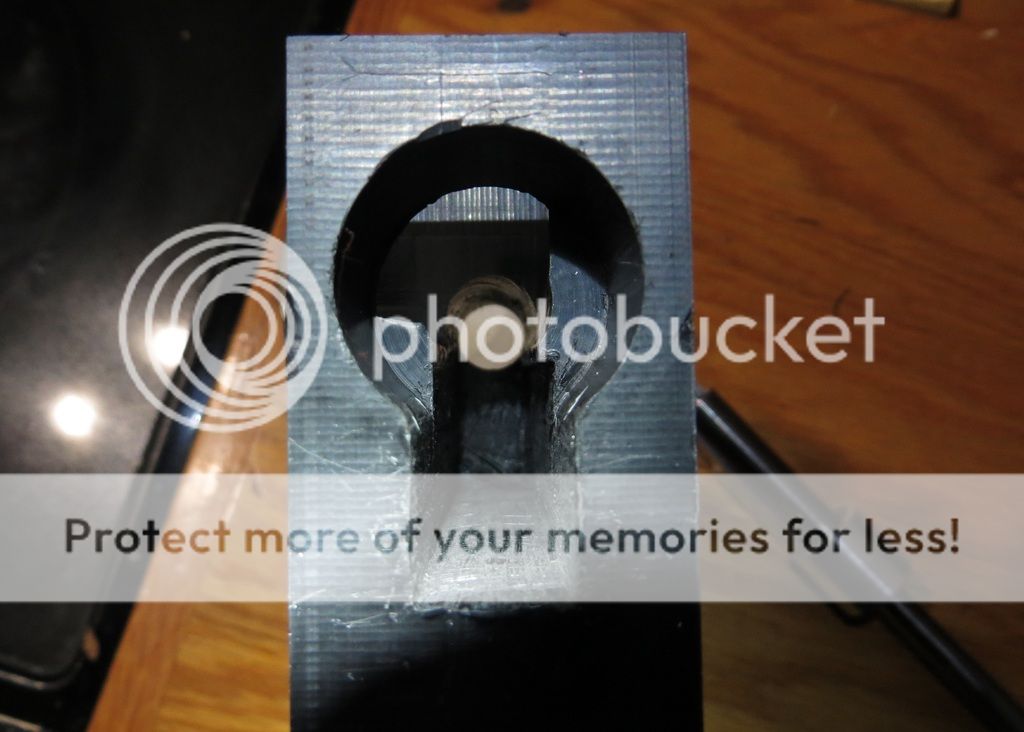
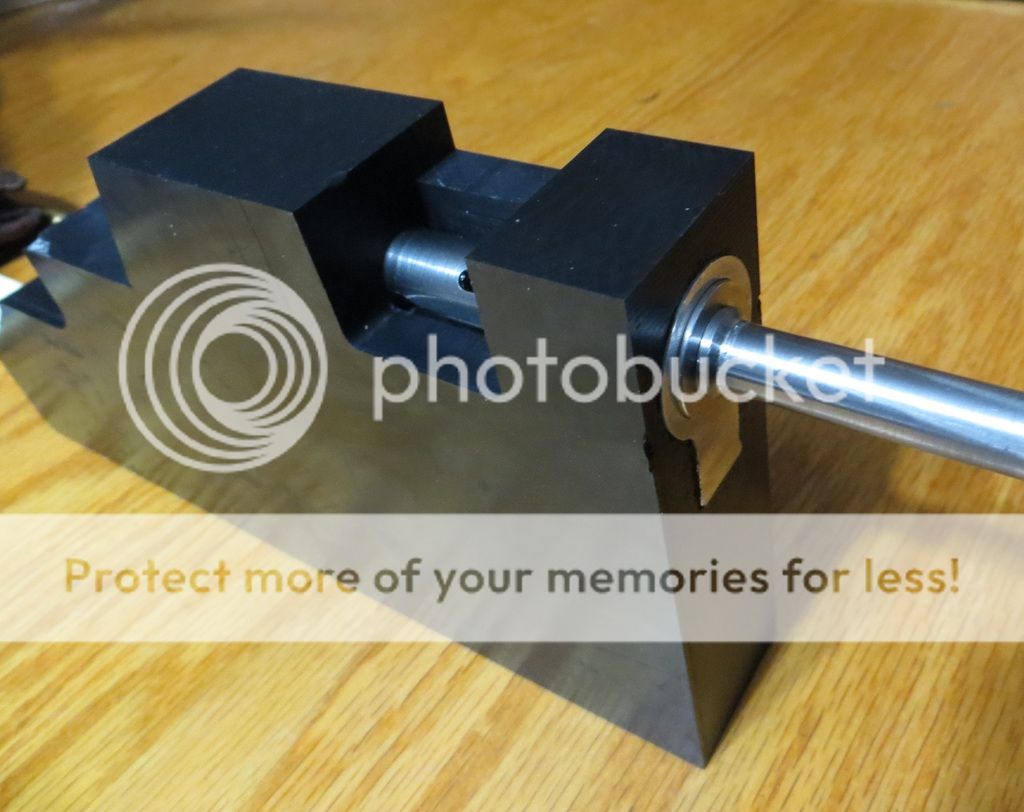
After profiling the receiver, I broached the bore for the bolt lugs with the bolt itself (before welding the handle on), then used the tilt/swivel vise to cut the handle channel
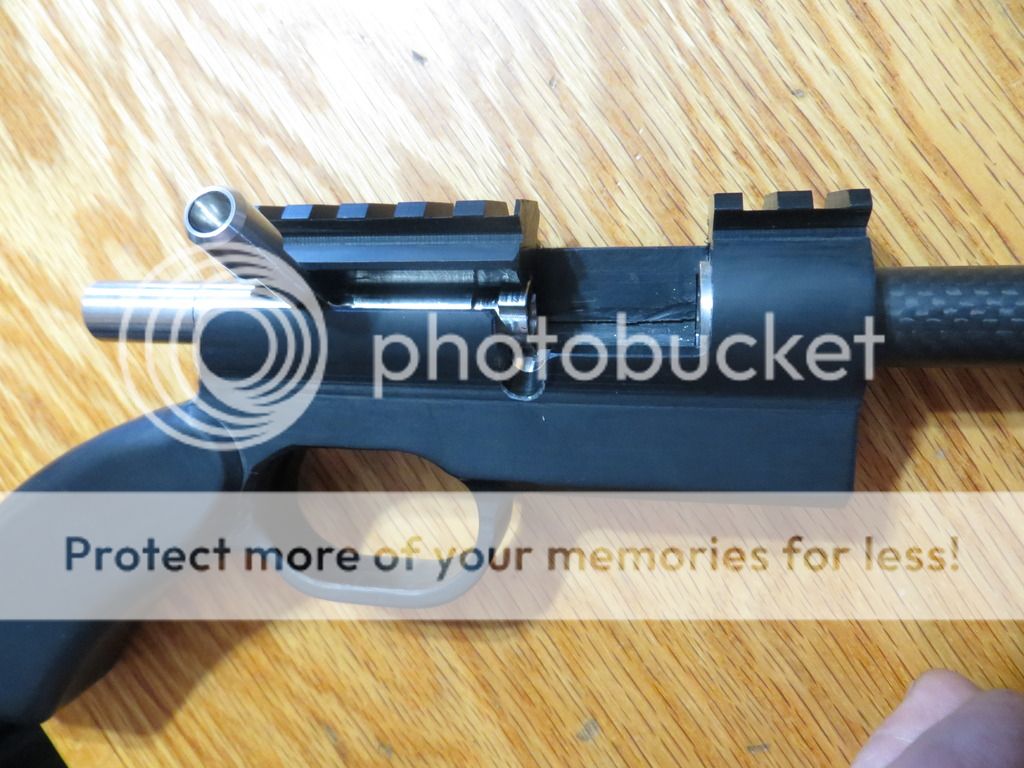
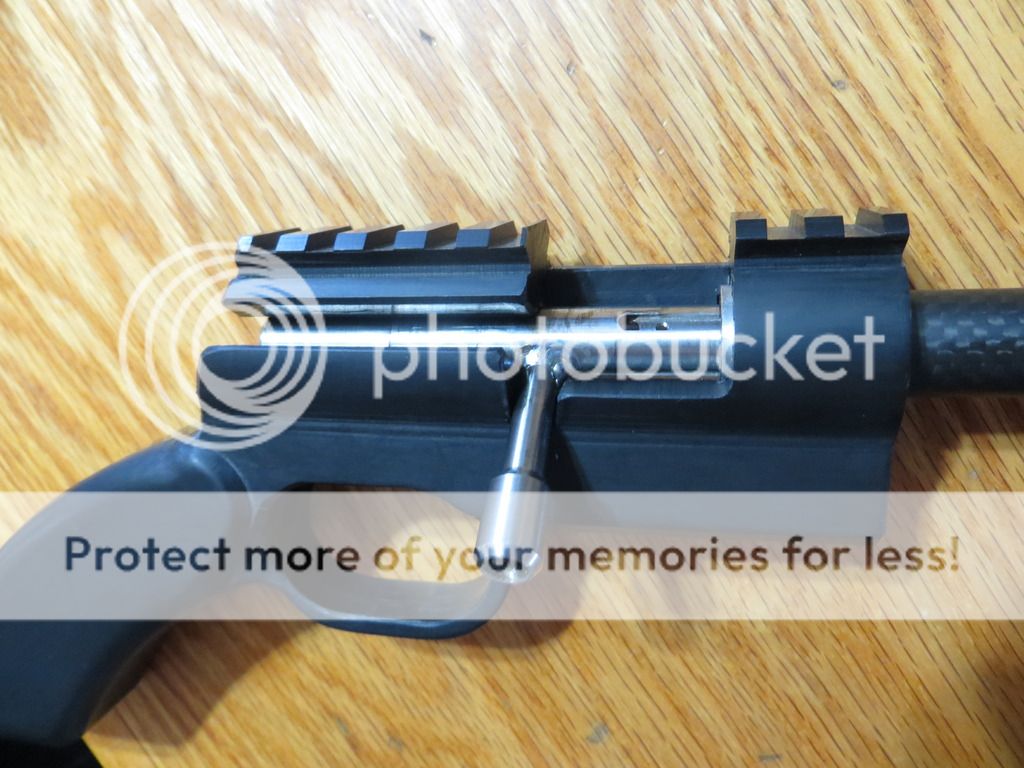
And this is where we're at now, just needing striker, trigger, sear, mag catch and a few other small parts and cuts:
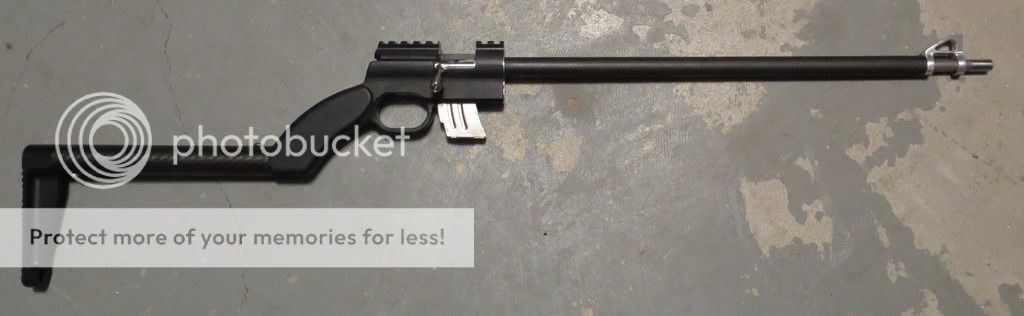
And taken down:
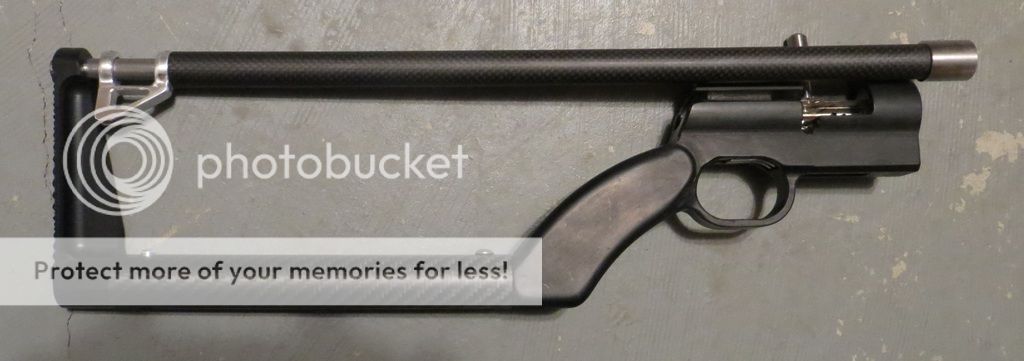
The height of the buttstock to the receiver looks a little awkward, but it's actually not bad at all when holding the thing. Can either use a low cheek weld, or rest your cheek on your firing hand, just behind the thumb.
The barrel assembly will be held to the receiver with a simple stainless sheet metal clip that engages the Picatinny slots.
Is 31.25" with a 16.5" barrel. 16.5" long, 5.4" tall and 1.25" wide at the receiver when the bolt knob is up in the stowed configuration. Current weight is 18.2 ounces, which I expect to increase to 20.7 with the additional parts, very close to my 20 ounce goal
Last edited: