tpelle
Member
I have three Pietta 1860 Army .44 revolvers. The oldest one, about 10 years old or so, has a few issues, mainly a too short arbor. The last two, however, bought over the last couple of years, are quite well made, with correctly-fitting arbors, and good timing.
I am willing to "sacrifice" my oldest one to Gods of De-Farbing. I would like to use it as a practice piece so that I can develop my technique, which may then be applied to the newer pair. Mainly I would like to remove the "Blackpowder Only" roll mark on the left side of the barrel, and the Pietta roll marks on the right. The Italian proofs don't really bother me, and let me make it clear that I'm not trying to pass the pistols off as originals. I would just like them to look a little more original.
So, does anyone have any tips or instructions as to the best way to do this - keeping in mind that I don't have access to any more sophisticated tools than a ball pein hammer and a flat file?
Also, there is one other seriously non-authentic feature to Pietta 1860 revolvers, which I will illustrate with the following pictures that I snagged off of the web.
First, an original Colt 1860. Note the shape of the barrel lug in the area between the wedge and the cylinder.
Now, here's a Pietta 1860. Notice how the barrel lug in the same area does not display the smooth curve, but is abruptly cut at more of an angle.
I wonder how difficult it would be, since I have to re-finish the revolvers anyway (and may do an antique finish while I'm at it), to re-profile this area using only a set of files?
Any advice, warnings, or suggestions will be appreciated.
I am willing to "sacrifice" my oldest one to Gods of De-Farbing. I would like to use it as a practice piece so that I can develop my technique, which may then be applied to the newer pair. Mainly I would like to remove the "Blackpowder Only" roll mark on the left side of the barrel, and the Pietta roll marks on the right. The Italian proofs don't really bother me, and let me make it clear that I'm not trying to pass the pistols off as originals. I would just like them to look a little more original.
So, does anyone have any tips or instructions as to the best way to do this - keeping in mind that I don't have access to any more sophisticated tools than a ball pein hammer and a flat file?
Also, there is one other seriously non-authentic feature to Pietta 1860 revolvers, which I will illustrate with the following pictures that I snagged off of the web.
First, an original Colt 1860. Note the shape of the barrel lug in the area between the wedge and the cylinder.
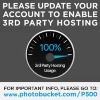
Now, here's a Pietta 1860. Notice how the barrel lug in the same area does not display the smooth curve, but is abruptly cut at more of an angle.
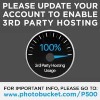
I wonder how difficult it would be, since I have to re-finish the revolvers anyway (and may do an antique finish while I'm at it), to re-profile this area using only a set of files?
Any advice, warnings, or suggestions will be appreciated.