I mounted a set of Talley rings on my Anschutz 1517MPR. During my last p-dog outing the scope worked loose.
www.talleymanufacturing.com
I've used this type ring on 3 Anschutz. On one occasion I twisted too hard and broke the screw, thus requiring it to be drilled out, which is why I was timid when I mounted this scope and didn't get the screws tight enough. Now I have a torque wrench, but cannot find specific guidelines. The Talley site says 17-20 lbs of torque for the cap screws, but say nothing about the base. Would it be the same?
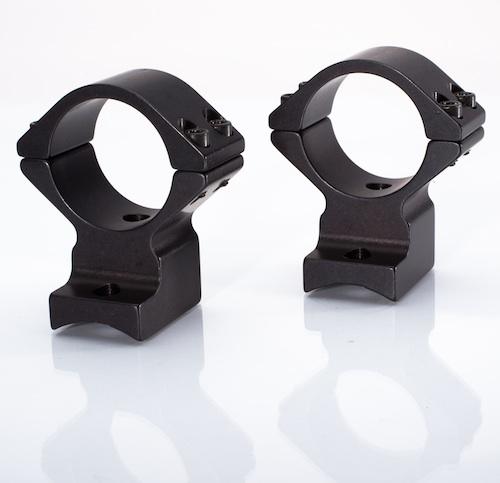
Anschutz Scope Mounts for Drilled and Tapped Receivers
Made in America, these Anschutz Scope Mounts made by Talley Manufacturing offer a unique and simplified one-piece scope ring and base

I've used this type ring on 3 Anschutz. On one occasion I twisted too hard and broke the screw, thus requiring it to be drilled out, which is why I was timid when I mounted this scope and didn't get the screws tight enough. Now I have a torque wrench, but cannot find specific guidelines. The Talley site says 17-20 lbs of torque for the cap screws, but say nothing about the base. Would it be the same?